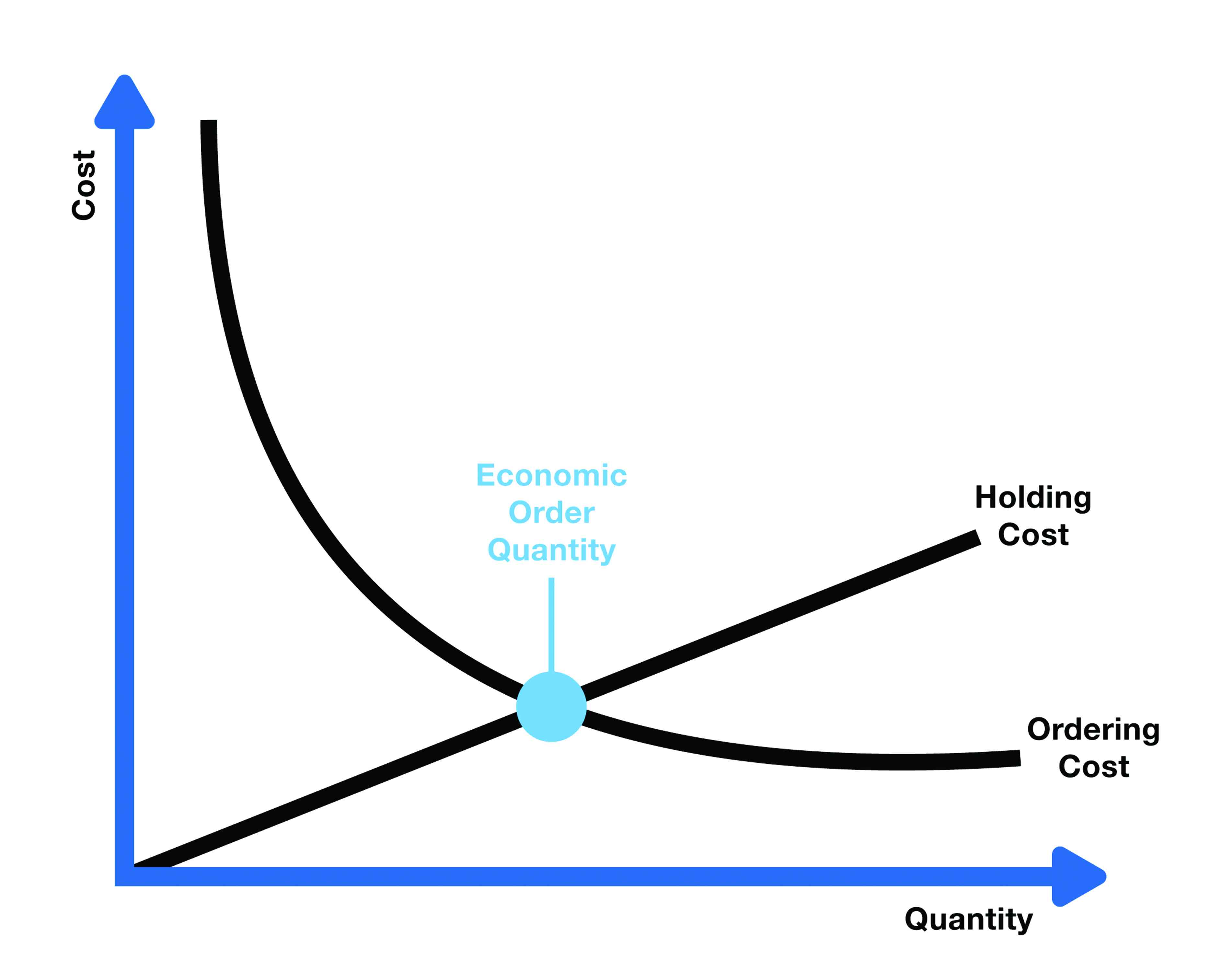
As customers demand ever shortening delivery times, the business community face increasing challenges over how to maintain optimum stock levels.
For expediency and completeness, supply chain professionals are required to ascertain the most cost-effective number of products the organisation should order as appropriate stock to hold at any given time.
The economic order quantity is the most ideal quantity that an organisation should ideally purchase with a singular view to meet consumer demand while at the same time minimising inventory costs such as holding costs, shortage costs and ordering costs.
This economic order quantity (EOQ) formula has been very useful in assisting procurement personnel to navigate the delicate trade-off between holding too much and too little inventory. Either problem will certainly create missed opportunities.
This tried and tested formula aims to find a balance where the combined costs of ordering and holding inventory are at their lowest. The model helps to find the sweet spot where the sum of these costs is at its lowest.
The EOQ formula is well-known for its capacity to determine the organisation’s inventory reorder point such that when inventory falls to a specified threshold, the system should be able to trigger the need to place an order for more units.
The ideal optimum order quantity will ensure that the inventory required will always arrive just in time to meet demand without incurring extra holding costs. The model’s enduring relevance stems from its capacity to balance two conflicting cost factors such as ordering costs and holding costs.
This will resultantly contribute to overall supply chain cost optimisation, ensuring that capital resources are not tied up unnecessarily in excess inventory or wasted in frequent ordering processes. If an organisation is constantly placing small orders to maintain a specific inventory level, the ordering costs will be on the higher side, along with the need for additional storage space.
- Emotional intelligence imperative in supply chain management (II)
- Cost to serve analysis: The holy grail of profitability (I)
- Cost to serve analysis: The holy grail of profitability (11)
- Increased focus on supplier diversity is the way to go
Keep Reading
The EOQ will therefore come handy by calculating the order quantity that minimises the number of orders placed, thereby reducing ordering costs by consolidating orders into larger, less frequent quantities.
The formula will assist in quantifying how much the organisation will require based on how much it sells in a given period of time, finding the middle ground between overstocking and understocking.
It is common knowledge that whenever your ordering matches your demand, there will be less products earmarked for storage which will lower real estate costs, utility costs, security costs and insurance costs.
By preventing overstocking, supply chain organisations will be in a position to avoid potential losses due to product obsolescence or potential pilferage. It must also be acknowledged that supply chains that are in a position to master their EOQ can navigate the complex interplay between inventory levels, customer satisfaction levels and cash flow with greater ease and confidence.
Supply chains will therefore ensure that the most popular commodities are always available on the shelf while reducing the risk of overstocking less popular products, which could lead to costly markdowns and or disposal costs. This is particularly more applicable to industry verticals with high product turnover such as fashion or electronics.
For many organisations, inventory could easily be the largest asset, and it often comes with a lot of ambiguity. The frequency of supply disruptions has highlighted the importance of maintaining optimum levels of inventory.
Growing economic uncertainty has compelled organisations to stock more inventory than they would do under normal circumstances.
In some cases, supply chains will either have too much inventory, tying up their working capital, or they may have too little, resulting in lost customers due to unmet demands.
The EOQ model will calculate more optimised order schedules which will assist in cutting down on obsolete inventory, especially for those organisations that hold perishable inventories that can result in dead stock.
Supply chain professionals will therefore sometimes feel as if they are walking tightrope. Where they lean too far one way, they may risk stock outs, where they lean too far on the other side, the possibility of drowning in excess inventory is for real.
Many organisations are therefore planning to replace just-in-time inventory with just-in-case inventory with a view to adapt to the ever-evolving business landscape.
The economic order quantity comes with many benefits. By consolidating orders into larger quantities based on the calculated EOQ, organisations can take advantage of economies of scale and negotiate better pricing structures and payment terms with suppliers.
The model will be useful in the reduction of lead times given the advance planning that comes with economies of scale.
The EOQ model is not only a tried-and-tested tool of trade, but it can be relied upon as a compass guiding supply chains through the intricate maze of inventory management.
It is not regarded as just maths; it is key to saving time and money. Procurement professionals will regard it as a safety net built into supply chain operations, helping to walk the perfect line between ordering costs and holding expenses.
It will therefore certainly assist in avoiding the frantic, last-minute scramble to restock. Organisations will develop more predictable ordering patterns, and the predictability will facilitate better production planning and resource allocation. These benefits compound over time, contributing to sustained competitive advantage and improved profitability.
The EOQ is a powerful tool but no magic wand. It has its boundaries. It is not without its pitfalls. It can stumble when faced with real world complexities.
Product life cycles have unique trajectories. Supply chain professionals are always at the mercy of economic health factors.
The EOQ model’s major weakness is that it assumes that demand is constant throughout the year. In the real world scenarios, this hardly holds true as demand often varies due to several factors, what with seasonal fluctuations and changing consumer demands being the most prominent.
The formula is based on certain assumptions that may not always hold in real world scenarios. It therefore fails to address real life challenges such as fluctuating customer preferences and dynamic shifts in supply chain.
Sudden changes in consumer preferences, market trends, and or external factors can significantly impact the accuracy of EOQ calculation, leading to potential inventory imbalances. This can lead to errors in determining optimal inventory levels in environments with large fluctuations in demand.
The EOQ can tell you when you should reorder, but it cannot help you if the supplier does not have what you are ordering. It also assumes instantaneous delivery which implies that replenishment of inventory is immediate at the time of purchase order placement. In reality, there is always a time lag between the placement of order and its delivery. Due to uncertainties in real world, late shipments or sudden supply chain disruptions, could pose serious challenges in the supply chain.
This can lead to stock-outs which can also result in lost sales and or dissatisfied customers. Without careful consideration and stress-testing of the underlying assumptions, the model could lead to unexpected problems. The EOQ model therefore requires a balanced approach that considers the benefits and limitations of the model and consciously tailors them to the unique circumstances of each business.
Supply chain professionals are fully aware that with inventory management, there is no fool-proof formula — even the EOQ is not fool-proof. It therefore comes with many other known challenges. There are prevalent unforeseeable circumstances that can affect your inventory balances due to spoilage, obsolescence and theft. Such variables will therefore render your previous EOQ less accurate and ineffective.
Another weakness is that the EOQ model is only appropriate when the inventory system is dealing with only one item. If the inventory system is dealing with multiple items, this model may not be the most ideal.
EOQ also assumes that the demand rate is linear, meaning it is the same every day, week, or month. This is rarely the case in real life and can lead to inaccurate results. There are times when using it can produce skewed numbers that misguide decision-making.
Another weakness is that the calculation of EOQ can be complex. The organisation may not have sufficient data for annual demand and other variables involved in the calculation. If the business still deals with spreadsheets or manual systems, data may not be readily available and may be low-quality or outdated.
The garbage in, garbage out rule therefore applies to all inventory management calculations — including the EOQ formula.
Inaccurate holding cost, inaccurate demand variables and inaccurate set up cost data leads to inaccurate final calculations. Organisations often struggle with inconsistent or incomplete data, particularly when dealing with new products or changing market conditions.
In conclusion, it must be noted that instead of relying on guesswork, EOQ gives you tangible numbers and proven calculations that suggest the best order quantity, transforming the formula into a practical powerhouse.
The formula appears to be a catchall solution to all inventory challenges. The model has become a supply chain staple.
We can glean insights that tell us which levers to pull and what our costs are across channels, giving a general ballpark understanding of how to balance the inventory equation. But as is always with any business concept, there is always the downside. The real magic happens when the EOQ formula integrates with other supply chain inventory management solutions.
- Nyika is a supply chain practitioner based in Harare. — [email protected].